When Shell UK challenged one of its NDT inspection contractors to develop a new asset based remotely operated vehicle inspection tool, JF Subtech was able to provide the specialist subsea insight to turn it in a highly viable project.
In recent years, Shell in the CNNS (Central and Northern North Sea) has moved away from using vessel deployed Remotely Operated Vehicles (ROV) for annual subsea platform riser and structural inspections in favour of Asset Based ROV (ABROV) deployment – provided by JF Subtech – to reduce execution costs.
Project completed: 2017
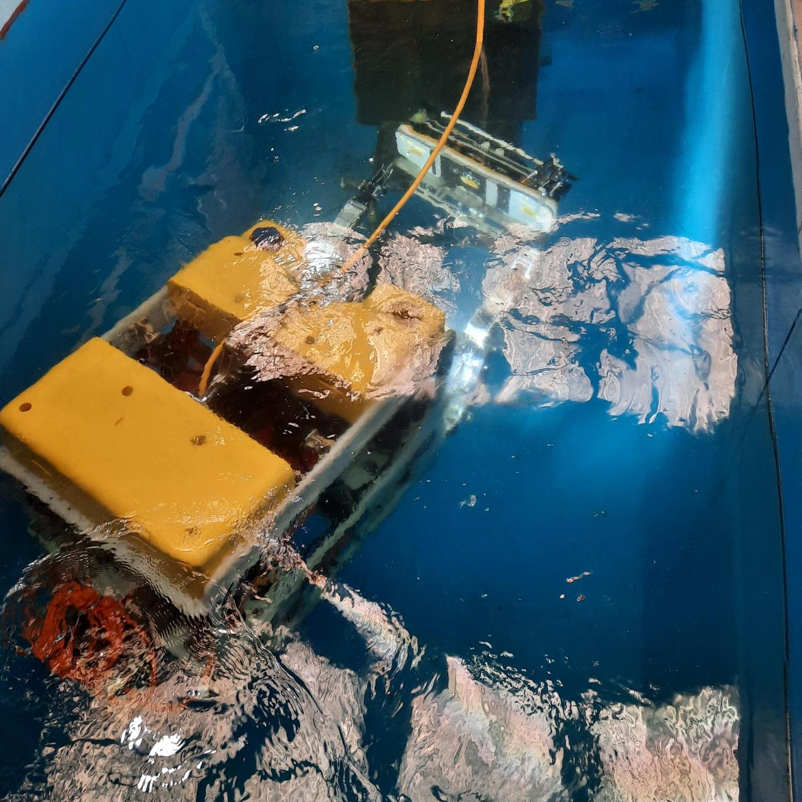
The challenge
- Shell UK needed to carry out comprehensive caisson wall thickness inspections across a number of its assets in a very tight three-month timescale.
- Existing technology was designed for use on a Work Class ROV (WROV), which required deployment from a vessel (ROVSV).
- To incorporate the wall thickness inspections into the ABROV campaign, a system capable of deployment using an Inspection Class ROV needed to be developed.
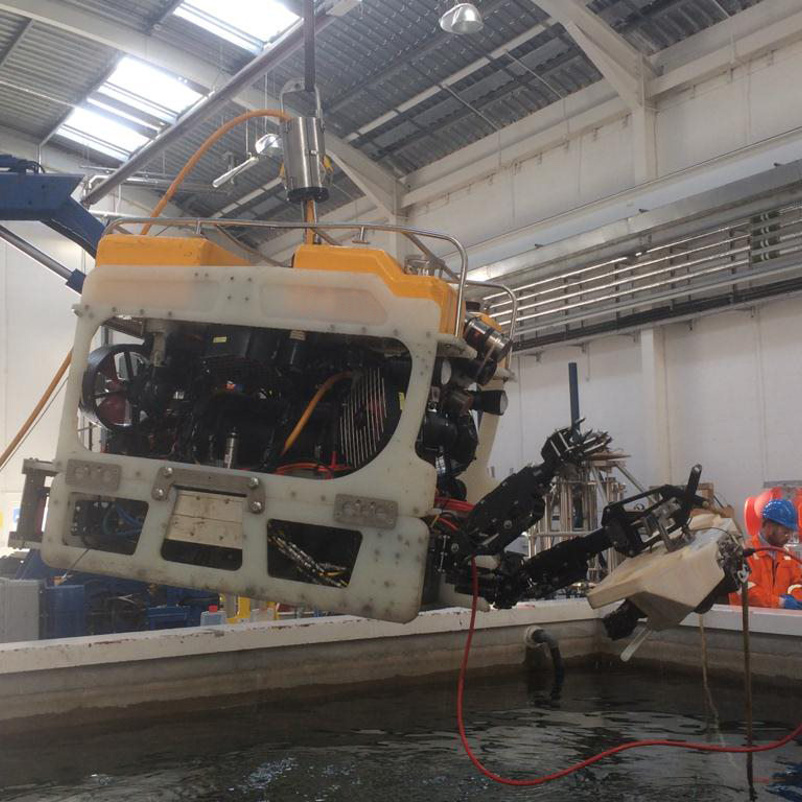
The solution
- Having identified an NDT inspection contractor, Shell approached the company to develop a new system capable of the inspections. An existing topside inspection tool, the Raptor, was identified as the basis of the modifications due to its size and fast scanning ability.
- The contractor has a good track record of underwater inspection tools, but none that could be deployed using an Inspection Class ROV. JF Subtech was brought in as a collaboration partner on the project.
- JF Subtech provided input into the interface requirements between the Raptor II tool and the Cougar XTC ROV system and, subsequently, conducted wet-testing at University of Aberdeen’s test tank facility, Oceanlab, to test both the physical and electrical interfaces.
- The wet test included deployment of the new tool to a test piece in the tank, and resulted in modifications which would ease ROV deployment prior to being mobilised offshore.
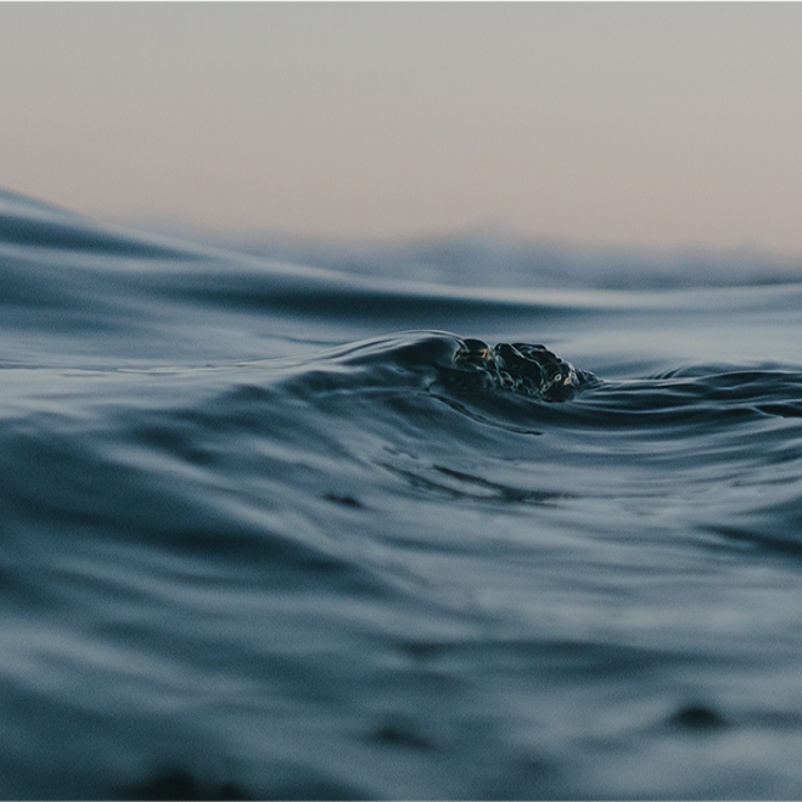
The results and benefits
- The inspection campaign proved successful in providing wall thickness data across three of Shell’s offshore assets. While the final product worked effectively and provided vital information on the integrity status of the caissons.
- The collaboration has resulted in the removal of the requirement for an ROV vessel for carrying out this type of inspection work, and allowed significant cost savings to be made. Now a proven tool can be used on other assets when required, removing future requirements for ROVSV when similar scopes arise.
- The work has proven the capability of the ABROV to deploy technologies that previously could not, opening a range of opportunities going forward.